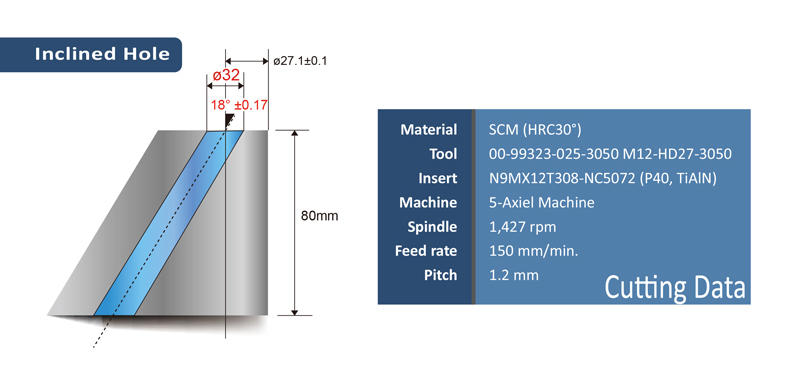 |
|
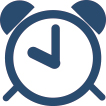 |
Time Saving |
|
|
|
|
Reduce machining process from 4 tools to 2 tools |
|
|
|
|
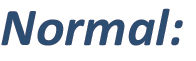 |

|
|
|
|
|
OP 1 : Apply to a flat surface OP 2 : Drilling OP 3 : Rough Boring OP 4 : Finish Boring
Machining time: 25mins. |
OP 1 : NC Helix Drill OP 2 : Finish Boring
Machining time: 7mins. |
|
|
|
|
|
|
|
|
|
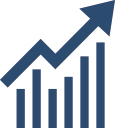 |
Results |
|
|
|
|
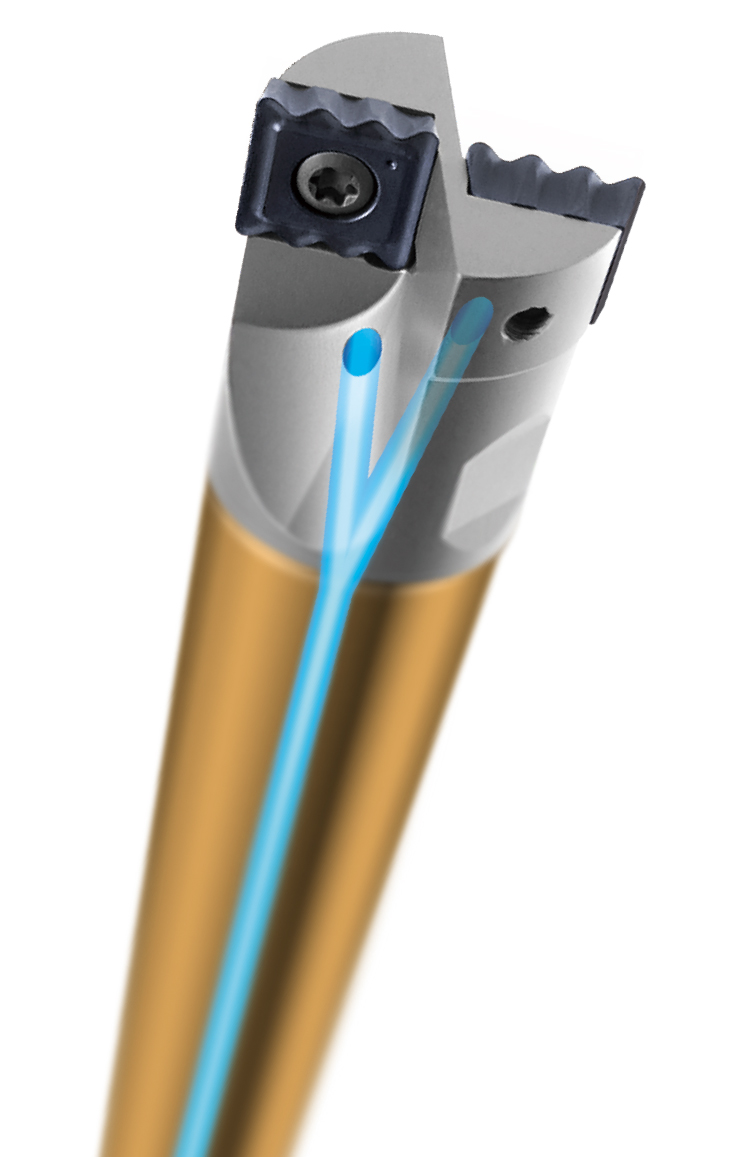 |
For machining an inclined hole, it normally needs a milling process to produce a small flat surface before drilling, and the straightness of inclined hole is always an issue that it is not easy to produce than any other conventional drilling.
NC Helix Drill is truly a multi-functional tool which is capable of helical interpolation for milling, slotting, and drilling. Small cutting load, low spindle power and special serrated cutting edge help to generate an inclined hole while maintaining an accurate diameter and straightness, also leads to a higher surface finish.
Only needs 6 tools for drilling holes from 13 to 65mm. Reducing your tool inventory greatly and machining time. |
|
|
|
|
|
|
|
|
|
|
|
|
|
|
|
|
|
|
|
Application in Automotive Parts |
|
|
|
The ability of NC Helix Drill is to work quicker, smarter that has made them best for reducing the operation. Additionally, the machines have higher productivity because it shorten the cycle time and eliminates the changeovers. |
|
|
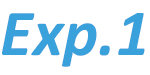 |
Forged Aluminum for Car Wheel |
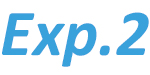 |
Balanced Ball Joint |
|
- Tool saving: from 4 to 2 tools.
- Reduce machining time by one operation.
|
|
- Tool saving: from 4 to 2 tools.
|
|
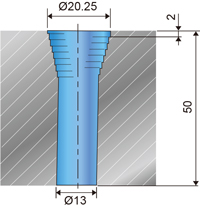 |
|
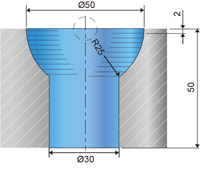 |
|
|